MBA Polymers has acquired the former Plasgran site in Manea Road, Wimblington, and recruitment for more than 20 roles is under way.
Last year Plasgran suffered damage to its Wimblington site when fire broke out.
Earlier this year the company announced its closure with some jobs relocated to other sites owned by its owners, Berry Global Group.
Now a deal has been struck for the site to be acquired by MBA Polymers
MBA Polymers UK says its new technologically advanced site in Wimblington “is a pivotal step in its mission to establish a comprehensive nationwide plastic recycling network, amid increased customer demand for lower carbon products”.
A spokesperson said: “The new site is an important milestone in MBA Polymers UK’s ambitious growth strategy.
“Leveraging years of plastics recycling expertise and tried-and-tested technologies, the site will accelerate the company’s ability to produce 100,000 tonnes of recycled plastics for its customers by 2030”.
MBA Polymers says it will take plastic bound for landfill and transform it into high quality, recycled polymers.
“This expansion will not only enable MBA Polymers UK to supply a higher volume of these recycled polymers to meet the demand, but it will also support the company’s growing product portfolio, as it increases its colour range,” said the spokesperson.
Manea will be MBA Polymers UK’s fourth location in the UK, joining its original Worksop site in Nottinghamshire, a separation line in Dover acquired in 2019, and the Duddeston site in West Midlands, established in 2022.
The Cambridgeshire plant will be operational from September 2023, creating 23 new staff positions.
Paul Mayhew, general manager of MBA Polymers UK said: “We are delighted to announce our new facility in Cambridgeshire as the next exciting chapter in MBA Polymers UK’s story.
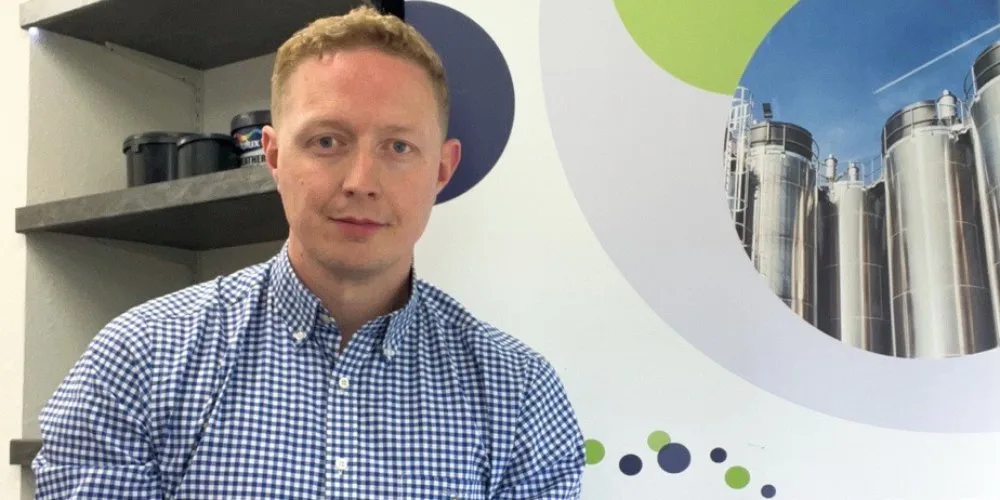
“Manufacturers know all too well that changes in regulations, consumer behaviour and the impact on the environment, means that increasing recycled content of products and creating circular products is now essential.
“The establishment of our fourth facility will significantly amplify our recycling capacities by 35%, diverting tonnes of plastics waste from landfill and providing high-quality recycled polymers back into the circular economy.
“We are dedicated to working with our customers to help them reach their sustainability goals, whilst keeping our carbon footprint to a minimum, in line with our ambitious commitment to become a net-zero business by 2040.”
TECHNICAL STUFF
MBA Polymers UK supplies a range of durable high-quality plastics, including recycled polypropene (rPP), polyethylene (rPE), polystyrene (rPS), and ABS to sectors such as electronics, vehicle manufacturing, and logistics management.
These materials contribute to carbon savings of between 75% and 86%, making them the first recycled plastics to achieve the Carbon Trust’s Low CO2 certification.
MBA POLYMERS HISTORY – IN THEIR OWN WORDS
That simple realisation is what prompted Dr. Mike Biddle to create MBA Polymers in 1992. Decades later, we operate two of the most advanced plastic recycling plants anywhere in the world.
Millions of tonnes of plastic is discarded each year, wasted, buried and burned. If it’s replaced with virgin polymers, that requires consumption of fossil fuels, more petrochemical extraction and processing, and more carbon released into the atmosphere.
Dr. Mike Biddle realised that if a reliable recycling process could be perfected, plastics destined for the landfill could be reclaimed, turned into valuable polymers, and reinserted into the supply chain.
So he set to work on perfecting that process.
Humble Beginnings
Armed with the determination to change the world, Dr. Biddle began work in his garage, seeking a commercially viable way to take plastic from complex waste streams and refine it into high value polymers. An innovative alternative to virgin polymers, for use in a range of applications.
By 1992, Dr. Biddle had proven the viability of his process. In 1997, our first small-scale pilot production facility opened in Richmond, California.
Plastics from a variety of complex waste streams were being converted into high value polymers including ABS, HIPS, PP, Filled PP and HDPE. A viable alternative to burying and burning had been found.
Expansion
Production facilities were first established in Austria and China, these plants focused on manufacturing three polymer grades from Waste Electrical and Electronic Equipment (WEEE).
In 2010, our largest production facility was opened in Worksop, UK to allow us to collaborate with one of the world’s largest metal recyclers – European Metal Recycling (EMR Group). Applying the knowledge gained and enhanced technology, MBA Polymers UK strengthened their product offering by being able to process even more complex post consumer waste streams such as Automotive Shredder Residue (ASR).
EMR Group would process end-of-life vehicles and retrieve steel and non-ferrous metals. MBA Polymers UK would retrieve plastic residues from their shredding processes and turn it into recycled polymer products.
By securing a consistent, high volume supply of plastic feedstock, MBA Polymers UK could now service larger and larger clients, reducing reliance on emissions-intensive virgin plastics across multiple industries.
In 2019, MBA Polymers UK expanded the business further, in the acquisition of a post-industrial arm focussed on processing post-industrial plastics from the automotive industry including complex multi-layered parts and converting them back into high quality closed-loop resins. Enabling MBA Polymers UK to provide a total plastic waste management solution to the automotive and injection moulding sector.
Together We Can Accomplish Anything
In less than thirty years, our vision and commitment has taken us from a small California garage to a world leading recycling operation.
But our task isn’t complete. Millions of tonnes of plastic still goes unrecycled, leading to countless tonnes of CO2 emissions and an insatiable demand for petrochemicals.
Plastics are too valuable to burn, or to bury. MBA Polymers UK will work to ensure that every year, more and more of this valuable material is put to good use, supplying industries across the world.