Whittlesey is preparing itself for a massive expansion to an existing Incinerator Bottom Ash (IBA) and construction and demolition (C&D) waste management facility at the former Saxon Brickworks site. Currently the total permitted throughput allows for up to 250,000 tonnes of IBA inbound. This is combined with C&D waste to generate a total of 300,000 tonnes of IBAA as an outbound material.
Johnsons Aggregates and Recycling Ltd has applied to Cambridgeshire County Council to increase the permitted capacity of the plant to 614,000 tonnes per year comprising 460,000 tonnes per year of imported IBA and increase in the throughput of C&D waste to circa 154,000 tonnes per year.
IBA is the ash that is left over after waste has been burnt in an incinerator. Depending on the composition of the waste, IBA can contain a number of materials including metals, rubble, and concrete.
Dealing with it is big business – in 2022/23 for instance, and the year it opened its Whittlesey plant, Johnsons had a turn over of £48m and nearly £5m gross profit.
Johnsons application to the county council covers hours of operation, throughput of waste, stockpile heights, and HGV movements.
The site generates an average of 101 HCV movements per day but “allowing for backhauling and differing vehicle sizes” this will increase to 332 (166 in and 166 out) movements per day.
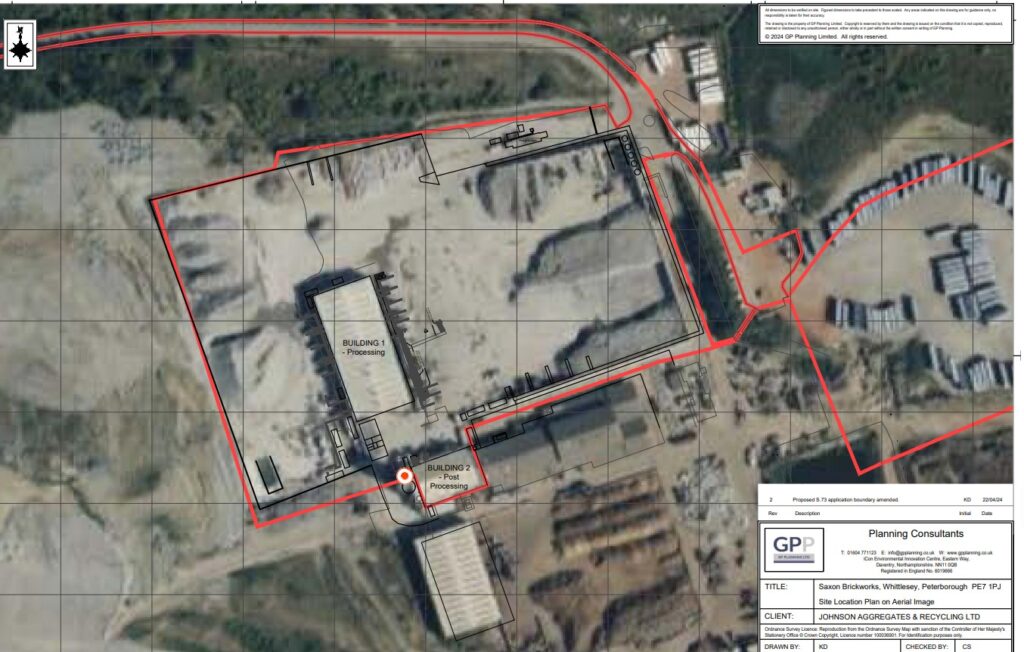
“The proposed increase in throughput volumes at the site is expected to contribute to additional employment opportunities and social benefits and subsequent local economic growth,” the company says in its application.
Expansion is expected to lead to a further 20 new employees taking the total number of full-time employees to an estimated 50.
Additionally, the proposed increase in volume throughput is expected to require up to 20 more HGV licensed drivers who may be employed by the applicant, or its contracted haulier(s).
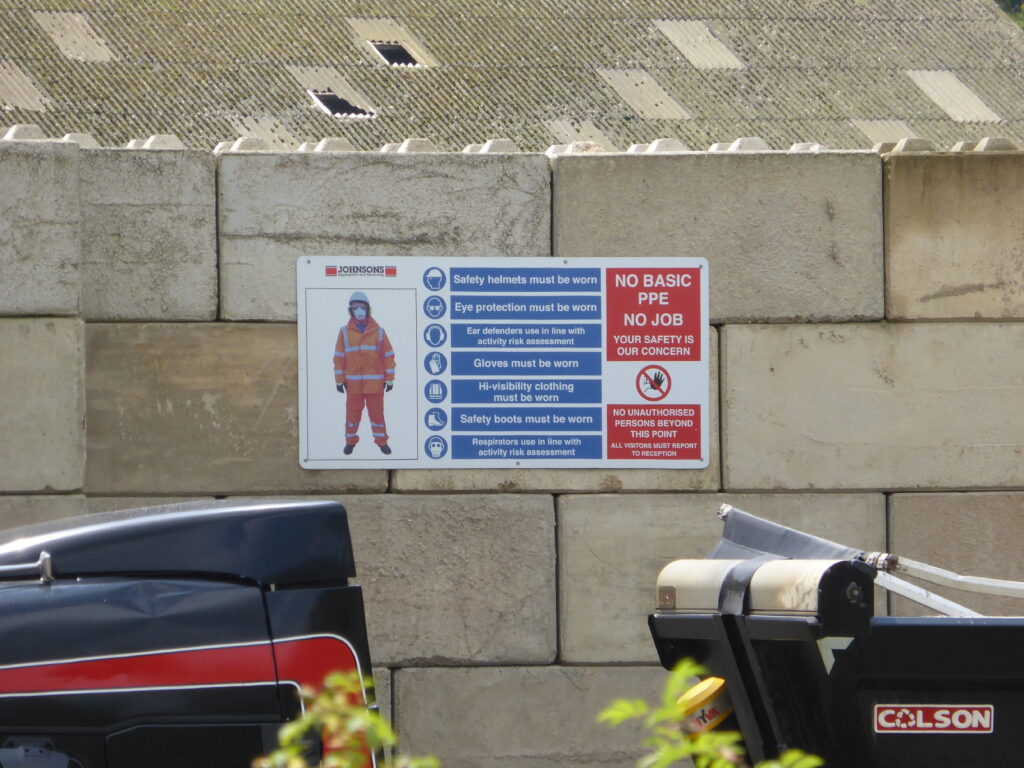
The site is located at the former Saxon Brickworks, off Peterborough Road, Whittlesey, Cambridgeshire.
Johnsons says a successful outcome will enable them to improve their operational flexibility and enable the recycling facility to accommodate IBA material from other Energy from Waste (EfW) plants as they become operational.
Johnsons reminds planners it is “an established company that currently undertakes the recycling of IBA at a recycling facility at Bunny, south of Nottingham and since 2014 at another facility in Ilkeston, in south Derbyshire.
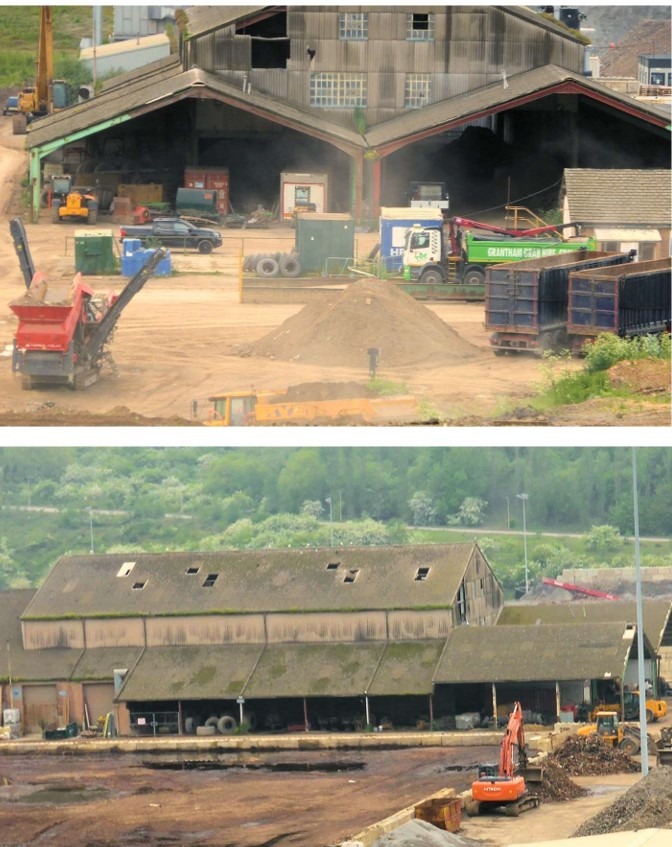
“These sites are fully operational and process around 100,000 tonnes per annum (tpa) and 350,000 tpa of IBA respectively, with a further 50 -100,000 tpa of C&D material being processed across the two sites”.
Johnsons has recently been granted planning permission for a further IBA recycling facility in Telford which will have the capacity to manage around 200,000 tpa of IBA material once it is fully operational.
The company explained that IBA is a non-hazardous material produced following the incineration of waste and is imported to their Whittlesey site directly from where the IBA material is produced.
“Prior to being dispatched from incinerator facilities within the region, IBA is required to be heavily quenched with water such that its content is as least 20% water,” it says.
“This is both to reduce its temperature and to minimise the risk of any air borne particles arising from its transport and deposit at a receptor recycling site.
“Upon delivery to the recycling site, the IBA material is deposited within the IBA reception and storage area. The material is then stored for a minimum period of 6 weeks during which time some of the added moisture is released as steam until the material is determined to be a suitable state in which it can be screened and processed.
“At this point the material still contains at least 10% moisture, sufficient to prevent dust emissions.”
C&D material is imported using 8 wheeled rigid HGV’s and after going over the weighbridge, is deposited, processed, and stored in the designated storage bays in the north-west corner of the site.
The C&D material is crushed and screened into various sizes and products dependant on individual client requirements using mobile plant.
The C&D processing takes place in the north-western corner of the site.
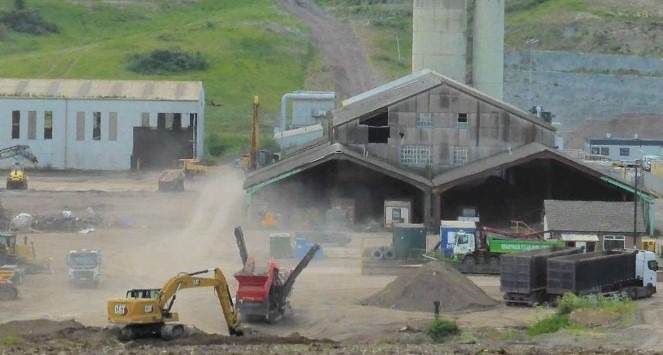
Johnsons says the IBA material requires a period of maturation, with frequent assessment taking place to determine the point at which it is suitable for processing and recycling.
At this point IBA is removed from the stockpile using a front-loading shovel and placed on a conveyor belt, via a hopper, through a trommel/screener that takes the material inside the proposed main recycling building on the site.
Within the main recycling building the IBA goes through a variety of machinery to sort it into various fraction sizes for ongoing processing to produce varying sizes of recycled secondary aggregates (IBAA).
The manufactured secondary aggregates are then taken from the building via conveyors or loading shovel either directly to storage bays or directly to HGV’s ready to export from the site.
“100% of the imported IBA is ultimately recycled either on site into IBAA or off site in the case of the metal elements which is sold to third party smelting companies,” says Johnsons.
The existing operations manage up to 250,000 tpa of IBA material and 50,000 tpa of C&D material.
IBA is imported directly from EfW plants on 27 tonne articulated HGV’s, whilst C&D material is mainly imported using 8 wheel rigid HGV’s.
“The majority of HGV’s seek to backhaul recycled material from the site reducing the impacts of HGV movements and increasing the sustainability and viability of the transport element of the operation,” says the company.
“In terms of HGV movements, based on a total throughput of 300,000 tpa and a 50 week operational year, a total of 506 HGV movements per week are required (253 in and 253 out), based on a 5.5 day working week, which would generate an average of 92 HGV movements per day (46 in and 46 out).
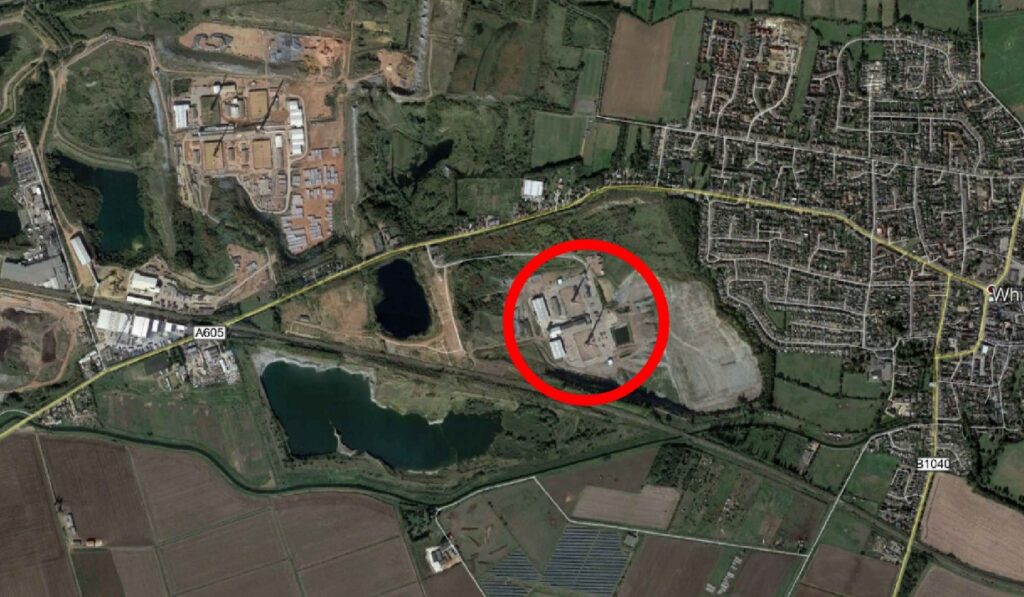
“These vehicle movements would be restricted to between the operational hours of the site Monday to Saturday and are restricted to when the weighbridge would be in operation. No deliveries or exportation of material would be permitted at any time outside of these hours.
“The IBA and C&D material is imported solely from the west of the site requiring all vehicles to turn right into the site from the A605 Peterborough Road.
“The IBA material is generated from existing EfW facilities across the region including Cambridgeshire, Bedfordshire, Buckinghamshire and Greater London if transportation to the Saxon Brickworks site is considered to be the most sustainable option for that material locationally.”
Johnsons claim their proposal “will demonstrably contribute towards sustainable waste management by moving waste up the waste hierarchy.
“The proposed increase in throughput of non-hazardous IBA waste to be processed and recycled as IBAA for use in the construction industry will divert waste away from landfill and enable the product to be recycled and reused”.
It says odour emissions associated with the proposed site “have the potential to cause impacts at sensitive locations” and they arrangements in place to tackle these.
“The health of the people living in Fenland is varied compared with the national average; child health is generally poorer, whilst adult health is better with respect to employment and crime levels, however poorer for harm, obesity and mortality,” says Johnsons.
“The proposed development will have a positive impact on health as it will offer new employment opportunities and encourage employees to adopt active transport modes as part of their commute.
“There will be some potential health disbenefits, largely from increases in HGV traffic, but for air quality, odour, and fugitive dust, it is judged that there will be no material change in the health of the existing population.
“Mitigation measures will be in place for noise and transport, including routing arrangements that can be secured by the imposition of planning condition(s). “
The company adds: “Taking into account the demographic of Fenland and the area immediately surrounding the site, it is judged that the proposed development will not disproportionately affect any specific vulnerable groups, for example, the elderly or children, in the population, nor will it have a significant impact on public health.”
Johnsons has put its noise assessment findings to the county council which “notes that the existing recycling facility has been operational for 2 years.
“Periodic noise monitoring has been carried out during this time, which has identified further measures to reduce noise above those considered at the time the previous planning application was submitted.
“Measures implemented to date have reduced noise levels from the operation of the site, which will be retained should planning permission for the extended working hours be granted”.
Other measures are also being introduced to “enclose the trommel (screen), which is presently external from the building and noted to be a main source of noise”.
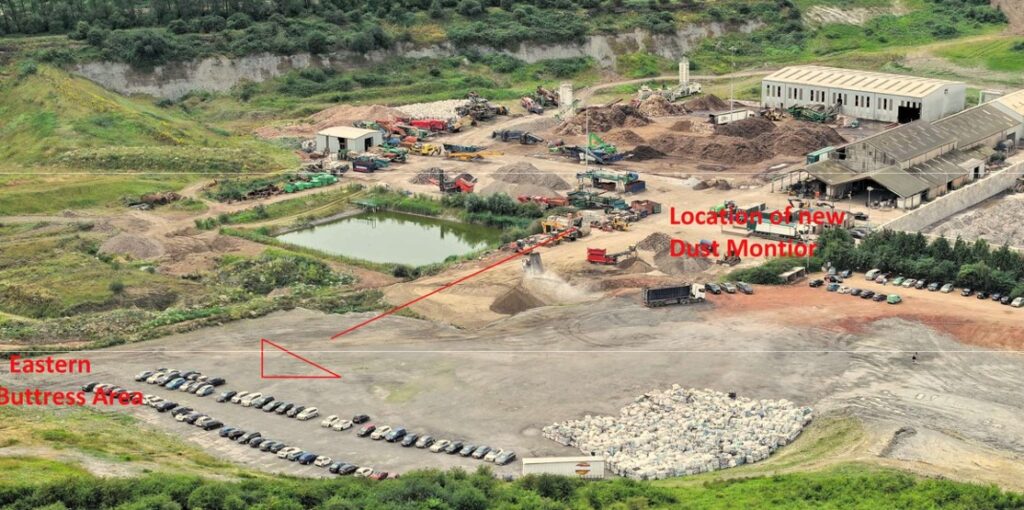
“Whilst several measures have been implemented to reduce noise levels from the present operations since the site commenced, further measures are proposed and discussed within this report, which will ensure that the noise levels at the surrounding properties do not increase above those presently permitted.
Johnsons argue that calculated noise levels show measures already taken and those proposed have resulted “in a clear reduction in the daytime noise levels at the surrounding noise sensitive properties, when compared to the noise levels calculated and assessed previously for the original planning application.
“This reduction includes consideration of the additional vehicle movements proposed during the daytime periods.
“Whilst not specifically assessed within this report, the mitigation measures implemented will also ensure noise levels are reduced during the evening periods, compared to those accepted previously, providing a clear benefit to the occupants of neighbouring properties”.
Johnsons conclude that use of the site is established, and they are simply asking to vary existing conditions “in part retrospectively”.
It adds: “The proposal will result in an overall reduction in carbon dioxide emissions, which will contribute to slowing down global warming and climate change through the reduction in greenhouse gas emissions.
“The proposal will also increase the use of recycled/secondary aggregates in the construction industry and is fully supported in planning policy terms, particularly where there would be a reduction in the use of land won aggregates, as there would be in this case.
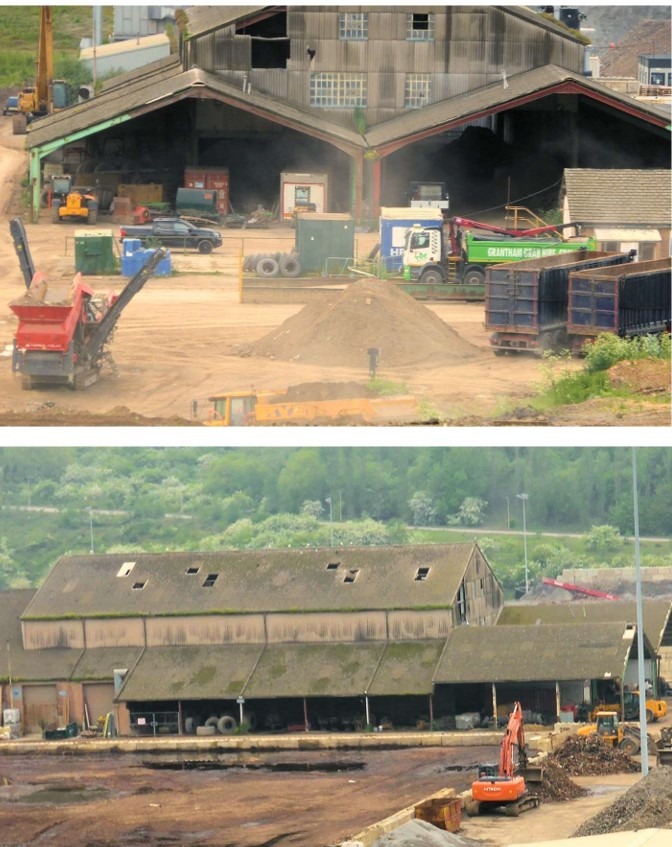
“In overall terms, the positive sustainable credentials of the proposal are matters which should be given significant weight in the planning balance.”
APPLICATION REF ON CAMBRIDGESHIRE COUNTY COUNCIL WEBSITE
CCC/24/091/VAR
(Comment must be received by early October)
GAIA
The Global Alliance for Incinerator Alternatives (GAIA) was formed in 2000 by organisations from around the world working independently on environmental justice issues. GAIA says it works on solutions-oriented efforts like “zero waste”; challenging international plastic waste trade; and addressing air pollution.
Here’s an abstract from one of their recent reports.
Bottom ash is fallout from the grate of mass-burn waste incinerators. Large quantities are produced, and this residue has negative value.
Visible proportions of sand, glass, and stones make it appear, on the surface, to be low hanging fruit for use in a circular economy; but bottom ash also contains appreciable quantities of toxic ‘high level of concern’ elements and persistent organic pollutants.
A secondary ‘fallout’ occurs when these substances leach from bottom ash into its surroundings across a range of conditions and timescales.
The waste incineration industry fails to mention these facts when advertising bottom ash as a ‘green’ building material. In comparison to direct airborne pollution from waste incinerators, bottom ash has gone somewhat under the radar, making it ripe for greenwash.
This report uses independent empirical research to evidence that incinerator bottom ash is insidiously hazardous and underregulated.
Risk is heightened by the fact that testing methods for its use as a building material are outdated.
A list of fifteen concerns for public health and safety is provided in relation to the use of waste incinerator bottom ash in cement-based products and as road/pathway aggregate.
Calls for the support of its use within a circular economy are premature, and, as per the precautionary principle, all ongoing usage should cease.
Examination of independently analysed bottom ash provides a diagnostic on the operational steady state of waste incinerators, incidentally, raising concerns about operational compliance with emissions legislation and the capacity of incinerators to produce benign bottom ash when fed with municipal solid waste.